
Improving facemasks for frontline COVID-19 staff
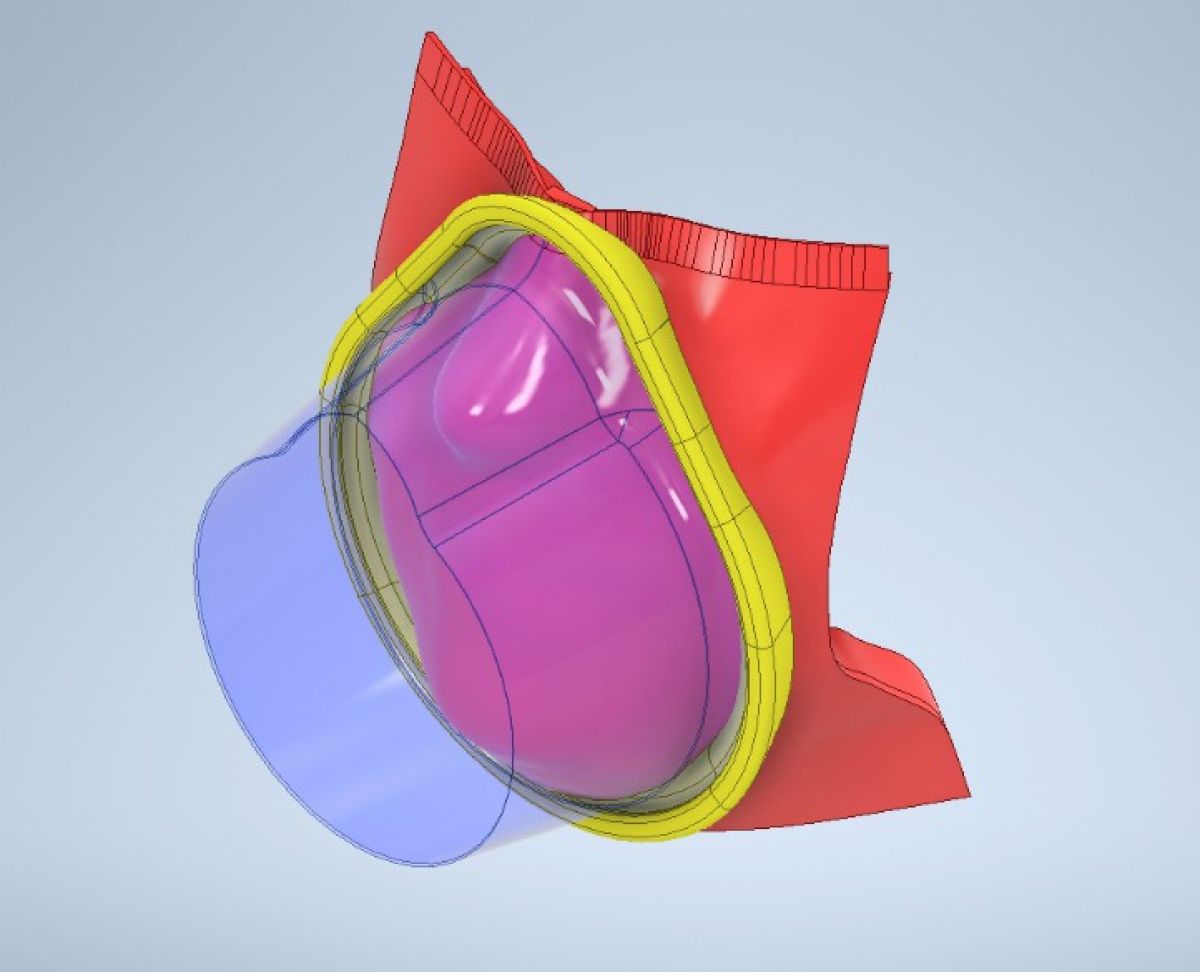
Scientists at Birmingham’s Healthcare Technologies Institute and King’s College London are working on a solution to improve the seal and fit of facemasks used in hospitals during the COVID-19 crisis.
Since the onset of the crisis, the subject of personal protective equipment (PPE) has become a key discussion point. Over recent days the focus has been on the supply of facemasks that allow healthcare workers to interact safely and perform procedures on COVID-19 patients. As the crisis continues to evolve, it is clear there are additional issues with prolonged wear of these masks, (i.e. abrasion and bruising of facial tissues) which has generated much interest on social media, with images of distressed healthcare workers circulating widely.
Drawing on the experience and ingenuity of the Academic Centre of Reconstructive Science at King’s College London, the teams have initiated a collaborative project to explore the feasibility of providing person-specific reusable, medical grade silicone seals to fit with the generic facemasks currently used in the NHS.
The silicone interface, which is being designed by researchers from the Centre for Custom Medical Devices at BHP founder-member the University of Birmingham, would help to improve the mask seal thereby reducing exposure risk. In tandem, personalisation has the advantage of reducing fitting time and improving comfort while reducing skin abrasions for NHS users.
Making use of the 3D capture technology at the Academic Centre for Reconstructive Science, individual faces would be digitally captured and the silicone seals 3D printed to fit the individual’s face.
Professor Owen Addison from King’s College London said: “We are exploring a number of novel approaches to improve facemask effectiveness. It is crucial we collaborate to push these vital projects forward, to better protect frontline healthcare workers during the pandemic.”
“Bringing together our collective expertise has enabled us to rapidly push forward these potential live saving innovations” added Dr Sophie Cox who leads the Centre for Custom Medical Devices at the Healthcare Technologies Institute in Birmingham.
“Our researchers brought together their 3D printing expertise and design knowledge to rapidly create a promising prototype customised mask seal.”
Led by Dr Trevor Coward and Professor Owen Addison from King’s College London, and Dr Sophie Cox and Professor Liam Grover from the Healthcare Technologies Institute at the Institute of Translational Medicine, in the past week their teams have:
i) Developed a promising approach to capture facial form digitally using a smartphone to provide a highly accessible method to complement their established 3D camera techniques that are used clinically.
(ii) Initiated computer aided design to identify how to fix a person-specific silicone face seal that matches an individual’s face to the periphery of masks being used by NHS workers.
(iii) Manufactured a prototype version of their custom interface ring capable of affixing on to a model mask.
Over the coming week, the team plans to begin 3D printing their novel design in silicone and conducting feasibility testing. The team which includes young UK scientists from the University of Birmingham; Luke Carter, Morgan Lowther and Dan Wilmot, are also looking at adaptions of their approach to develop new mask designs that could be manufactured quickly in a distributed supply chain and deployed during this crisis.